7月28日,主题为“闪耀数字经济新引擎”的2022全球闪存峰会(Flash Memory World)在线上盛大召开。
本次峰会特邀东北特钢CIO刘健以“传统企业如何实现数字化转型”为题,介绍了东北特钢在信息化的发展历程中,利用现有互联网技术和工业软件构建数字化车间的架构与数字孪生体,来解决企业发展中的困惑,把传统企业的信息化推向新高度的故事。他还介绍了如何有效地把沉淀的数据价值挖掘的经验与方法。
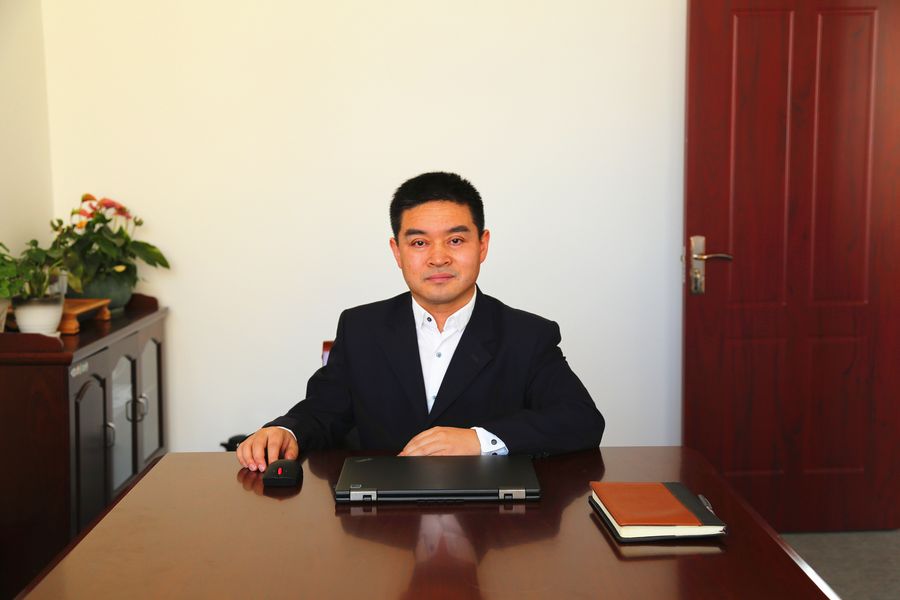
刘健:各位专家、各位朋友,非常感谢大会给我这次机会和大家一起交流“传统工业企业如何实现数字化转型”这个话题。 东北特钢集团是辽宁省大连市是中国传统的一家钢铁企业,也是中国最大单体的特殊钢企业。
东北特钢集团有着悠久的历史,是中国第一个不锈钢、第一炉高温合金钢、第一炉工艺钢的诞生地,也是中国“天宫”、“嫦娥”、“神舟”系列主要的原材料供应商之一。
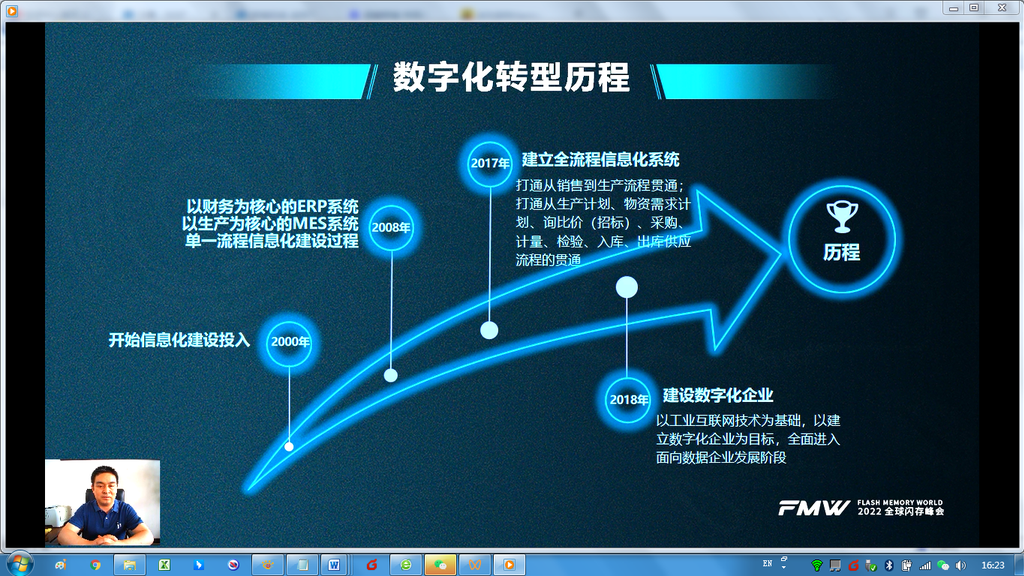
东北特钢信息化经历了三个阶段:
第一阶段,在2008年以前,东北特钢是以单体的ERP和MES系统,围绕着财务进行管理,主要集中在生产的计划排程和财务的核算上,没有达到数据的共享,也没有达到流程的节点的控制。
第二阶段,从2008年到2017年东北特钢的信息化进入到第二阶段,做全流程的信息流、物流和数据流的打通,主要实现从销售、下单到合同排查到生产入库,到合同交付全流程的管理,基本实现了信息化的全覆盖。
进入到2017年,东北特钢发现了沉淀了十几年的数据无法进行充分地挖掘,特别是工艺数据无法得到传承,产品制造过程无法得到有效的跟踪。
借助工业互联网的技术发展和大数据的发展,东北特钢不断地对数据重新挖掘,再创新的价值。自此东北特钢集团信息化建设进入了第三个阶段,就是数据的价值挖掘。
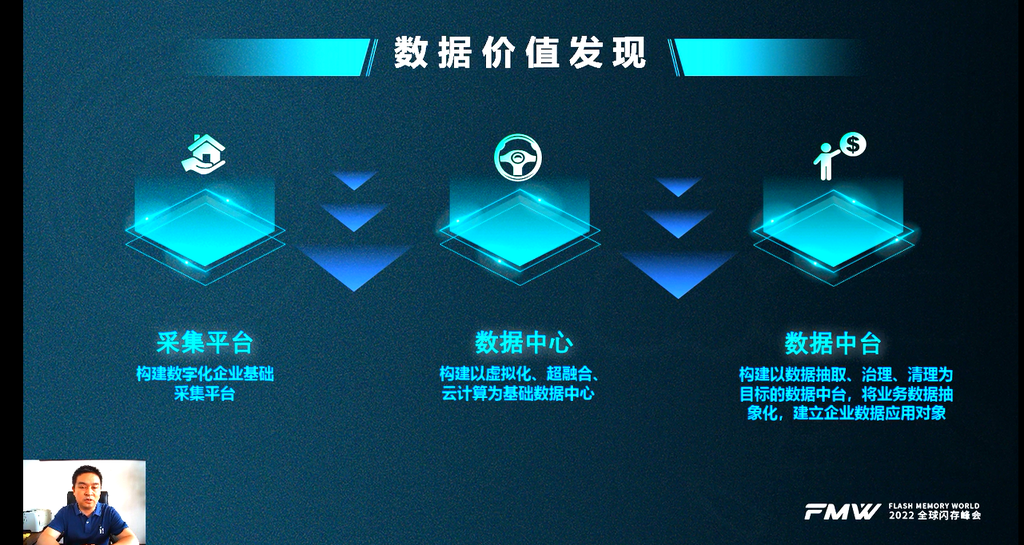
我们从三个方面把沉淀的数据价值有效的挖掘出来:首先建立了工业采集平台,把现有设备的工业数据都集中起来,以便于其他系统的共享、利于后期设备的运维、故障分析,随后建立了数据中台,把有价值的数据或者是主数据都纳入一个数据湖管理,三是通过虚拟化和超融合构建企业的私有云平台,实现数据集中存放、集中管理,解决了企业很担心的数据丢失或者其他故障造成数据损失的问题。
在此基础上我们构建了企业数字化架构,架构分四部分:
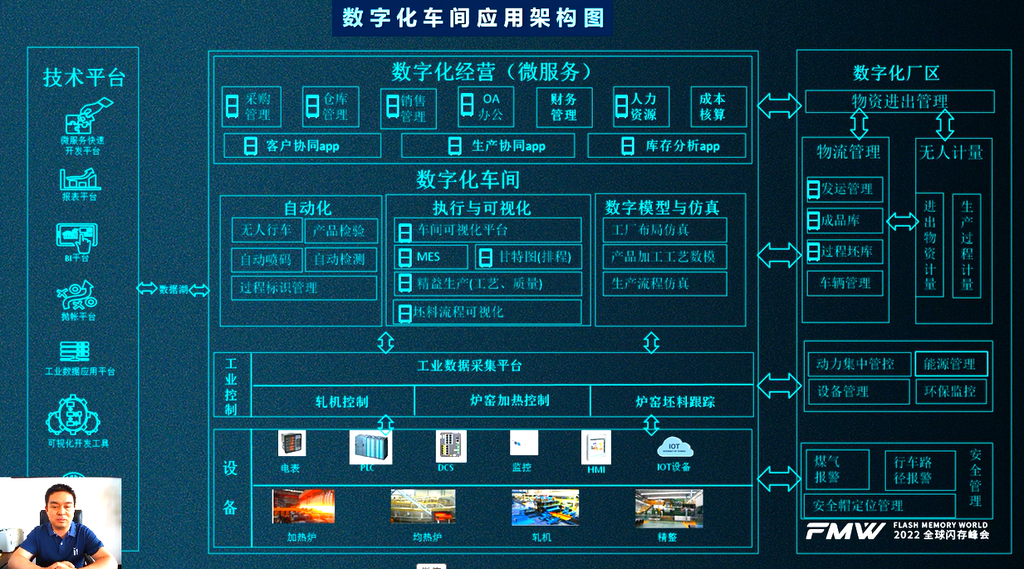
底层部分是数字化车间。数字化车间以基础自动化为基础,通过采集平台、控制系统和物料跟踪系统,将相关的生产数据和工艺数据、质量数据送到数字化车间的系统;数字化车间系统配置有MES、可视化系统、物料跟踪系统,保证了生产现场数据不落地,也保证了产品全流程的质量跟踪。辅助有配套的自动化系统无人行车、自动检测、产品标签跟踪、产品检验,还有配套的工艺模型、车间模型等等。以数字化为特征的数字孪生系统在此基础上就诞生。
企业经营数字化。利用微服务平台,利用现有的数据,利用报表工具和BI工具重新构建了企业的协同平台,比如生产协同、销售协同、采购协同,这保证了企业生产经营数据的一致性、连续性和可追溯性。
企业配套的数字化园区。智能物流系统和环保、安全管理系统,这也是企业核心。环保是企业的生命线,安全是企业的底线。没有这套系统,企业,特别是钢铁企业就无法做到节能减排,也无法做到生产的正常进行。配套当然还有技术平台,这也是数字化企业这几年很核心的一项技术,它综合了存储、系统、软件各项技术于一体。
我们打造这个信息平台,也保证了东北特钢的数字化车间和建立数字化企业能够有序地进行。
下面给大家展示基于这个思想和平台上我们做的三套系统:
第一,数字化车间。
炼钢车间把传统的MES管理的工艺标准、生产计划,能源系统的介质管理,消耗管理和物料跟踪,质量工艺管理的工艺卡、质量数据分析与生产现场炉台的关键点控制结合在一起,形成目前的数字化车间的统一管理平台。
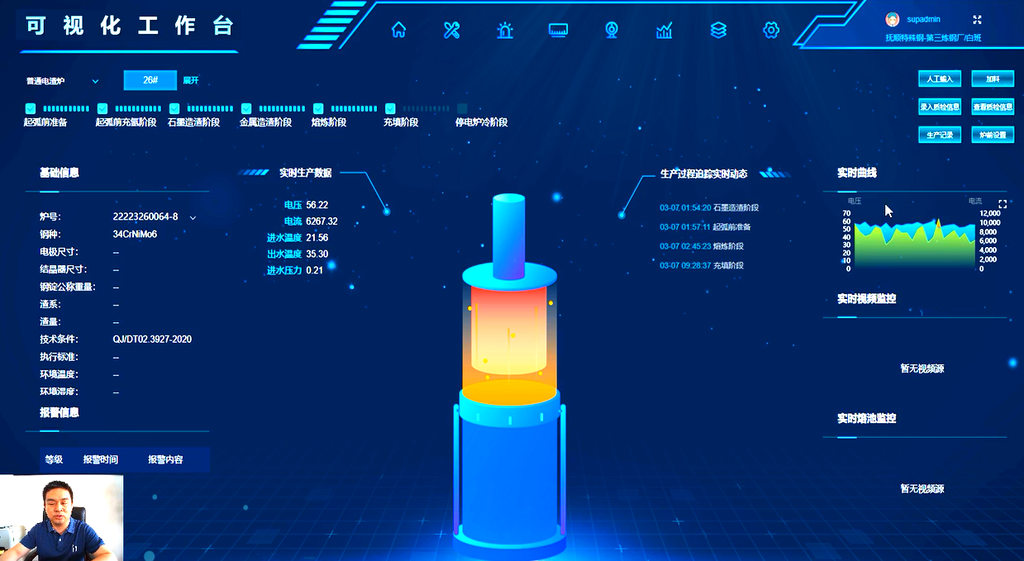
这是现场运行的工作台,这部分数据是生产这一炉钢的基本标准和基本要求,有这一炉钢的工艺路线,按照每一个步骤的可视化的形式展示给现场的操作人员。工艺控制要点数据来源于生产设备的实时控制设备,由这些设备根据这些指标,根据工艺卡的指标来控制这个设备的运行。一炉钢整个生产过程,每一个过程,每一个步骤都是进行系统跟踪,以保证产品的生产是有序,按照工序要求、工艺要求进行生产,同时在这过程中,可以看到它的加工生产曲线。
刚才看到的是系统,这个系统前提基础就是要构造的数字对象和数字孪生体。把这个车间都可以统一看成一个数字孪生体,有生产、质量、能源、消耗各项指标构成一个孪生体,将这孪生体进行数字表征化后,再进行实例化。
这是在系统中构建孪生体的一个模型。
从某一个车间开始,先构建孪生体的数字分支,在每个分支下再构建控制要点和属性。这些数据有一部分数据来源于现有运行的MES系统、能源系统以及生产过程控制系统,实际的结果要送到生产控制系统和全面质量管理系统以及数据分析系统。最主要的数据来源于底层基本自动生产设备,使核心产品生产可以实现现场和远程生产加工的模拟,并快速地将合理而且可靠的生产加工工艺,复制到下一个同类型的产品生产中。
第二,高炉集中管控平台。
它是把现场的自动化数据和MES能源包括加料系统进行统一整合一套系统,并融合了视讯平台,把现场的视频、图像和这个平台进行融合。
第三,产品生产过程全域可视化。
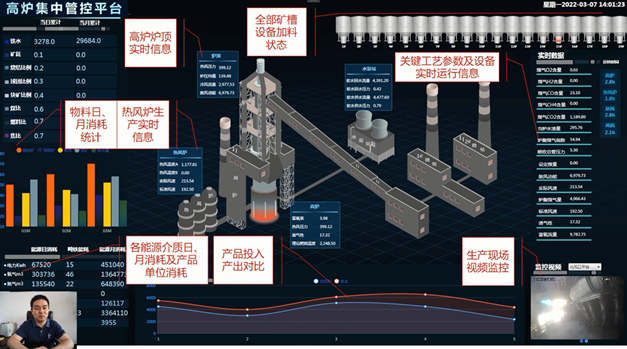
在钢铁企业的每一个车间,都是数百米长、数百米宽,生产管理人员无法很快地对现场的生产产生整体的概念。这样催生了工业数据采集平台以及数据中台,建立了全景可视化系统。这是一个车间的两条轧机,两个加热炉,十二个均热坑,加上冷床设备,都在一个全景的可视化平台上。生产人员或者是工艺技术人员、管理人员能够快捷掌握生产现场设备运行状况(不同颜色代表着各种设备的开动情况),还能了解到各个炉窑现在里面每支坯料,以及在冷床的打包情况,减少了人员在现场的流动,也提高了工作效率,各个系统能快速地联动起来。
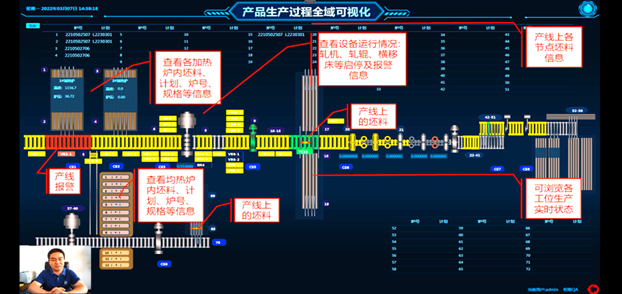
以上是我们在进行数字化转型过程中做的一些初步尝试,还需要很多工作要做,我们只是把各种数据收集、存储在一起。通过信息化和自动化两方面数据进行融合,满足了目前的一些工作。这离实现全面数字化,比如说无人化、黑灯工厂还有一段距离,但有这些基础系统和基础平台的搭建,已经实现了企业现场少人化、无纸化。
在信息化建设发展的新阶段,我们有很深的体会。
传统的工业企业要实现数字化,首先要利用现有的工业互联网技术和大数据技术构造数字化的模型,引进数字化企业的管理理念;原有的这种流程化的设计思想以及企业业务流程化的管理思想,要进入一个以数字单元为特征的单元化、有生命体的一个个数字对象,以数字孪生体为基础的数字化企业。
我认为,我们这几年用得比较好、对企业改变比较大的,对建立数字化企业影响比较大或者说没有它数字化企业就无法下手的,就是如何构建数字孪生体,也可把它叫做数字对象:通过把现场的每一道工序、每一个装备、每一个车间、每一个生产单元都抽象出来一个数字模型(有些系统叫做数字画像)。通过数字画像的过程构建实例,再通过实例与现场的设备(或其他信息系统)进行数据对接,构建数字孪生体。
如何构建这个数字孪生体?
我们主要是依托“I-DCC集中集控的管理平台”。这个平台功能很多,它主要的目的是把工业数据,也就是传统的结构化数据和现场的实时数据,都统一到一个平台进行重新定义、重新清理,数据进行统一命名、统一定义、统一开发、统一部署,让其他系统能快捷地获取到自己所需要的数据。
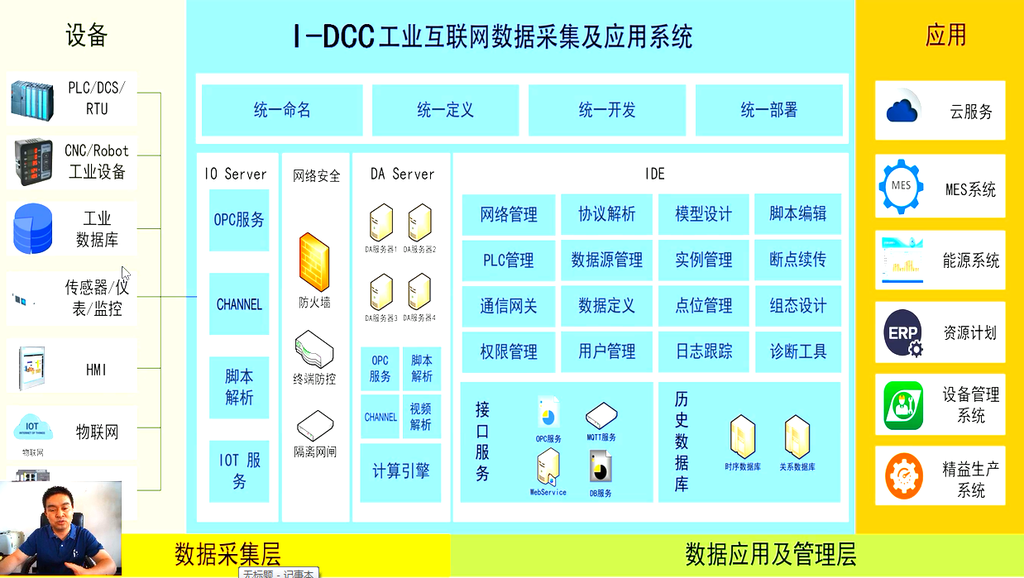
以下内容为视频举例,具体可参看视频直播。
首先通过I-DCC系统找到工作模板,引入数字模型,构建一个加热炉、一个转炉甚至构建一个视频。通过系统先建立基础模型,派生出其它模型,比如构造一个炼铁车间,炼铁车间构造完成以后,就可以把原来建立的基本模板通过拖拽方式拖入,相当于建立起了一个炼铁车间数字模型。当然这个描述相对比较简单,因为实际上的模型复杂的多,比如炼钢车间的生产、能源等,各种生产经营或者是装备的参数放在一个数据模型里。数字模型构建完以后,就是做数据模型实例化,实例化的过程就是将构建的模型与实体的数据进行联动。
模型构建完成后,可以再构建模型的分支,比如说这个模型有一个炉窑的加热时间、结束时间,炉窑的开始和结束时间对产品的加工很重要。
刚才做了一个数据模型,数据模型的数据如何与实际的装备数据或者其他系统的数据联动?这个视频就是展示一下,我们如何将实际的PLC数据或者工艺数据与模型数据进行联动的。首先要建立一个PLC的通讯,在这里, PLC的通讯就是IP地址、通讯协议,再把PLC每一个寄存器点位加入到PLC这个系统来。这一套I-DCC配点或者说打通工业自动化和信息化相对比较简单,自动化工程师、信息化工程师甚至管理人员都可以操作。找到原有的数字模型,配好PLC的点,再发布到服务器上部署,这样就完成了数据的打通。我们的管理人员或者是工艺技术人员,就可以看到现场某个设备和某一个控制要点的数据。
这就是构建数据模型,并将数据模型实例化的两个视频来展示它。
这是实际的一个逻辑图还有一个实物连接图,这是我们实施数字化工厂的一个感受。建立数字化工厂重要的是构建数字模型和数字对象,另一方面,还要导入什么叫数字化企业,如何建立数字化企业管理理念。其实数字化企业有区别于传统的流程化企业,有区别于传统的管理方式,它更多地把一个企业或者是一个车间、一个企业一个工序、一个装备放在无处不通、无处不连的一个数据节点上,由它自己这个节点上产生的数据与其他节点进行交换。
这就是未来建立数字化企业核心的内容:如何去构建企业的数字化模型。
今天给大家分享的内容就这些,再次感谢大会给我这次机会,把东北特钢这两年做的一些工作给大家进行交流分享。但我认为还是刚刚起步,做得比较肤浅,只是探索利用现有互联网技术和工业软件,能够把传统企业的信息化推向一个高度,解决十几年以前无法解决的问题,解决了企业发展中的一些困惑。
非常感谢大家,也非常感谢各位朋友和各位专家!